
Anjali and Vinod Barve’s horticulture-driven business is reaping rich dividends
By Samay Shetti
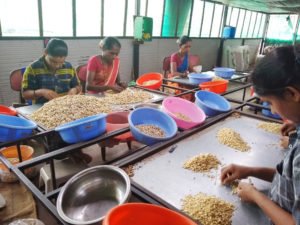
We live in a time where cities and urban centres are expanding their boundaries rapidly. More and more people are pouring into the cities in search of new avenues of income sources. Villages are turning into holiday spaces while agriculture is neglected. Which is why those who decide to take up an agrarian profession must be commended. In the lush green hills of Satode in Sattari, Anjali and Vinod Barve took up the family profession of agriculture and horticulture and are constantly upgrading and expanding to gradually cover fields.
Having acquired his bachelor’s degree in botany, Vinod decided to continue in the agrarian profession despite the pressure as well as the lucrative offers available. Soon, marriage with Anjali followed and the couple joined forces to start an adventurous journey of enterprise. Their growth through the years has been commendable, due to which Vinod Barve was conferred with the Krishi Ratna award on December 19, 2017 at Campal and also with the Sarvotkrusht Bagayatdar award by the Goa Bagayatdar Society in the same year at Ponda.
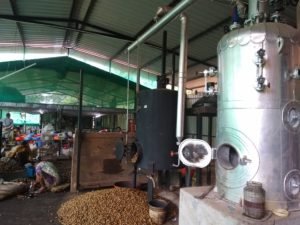
In the year 2011, Vinod ventured into the production of areca plates. These plates are made from the lower, dense part of the areca palm leaves (supari). The leaves are removed and dried; they are then punched and moulded into different sizes using a machine with dies of the required shapes and sizes. The dies are heated and pressed on the plates to mould the leaves. Initially, Vinod started the business with manual machines. The method was impractical in terms of commercial usage because of its time and labour intensive nature.” The manual machines were very tedious to work with, and the margins were too low and often loss-making,” says Vinod, “That’s when Amey Karmali from CIBA suggested I procure automatic machines With guidance from CIBA, we sourced the machines,” says Vinod. They sourced the machines from Salem, Tamil Nadu and, in 2012, started commercially manufacturing the areca plates with two machines, each costing ₹80,000. By 2017, Vinod had procured four more machines. The product is manufactured in three dimensions – four-inch bowls, 10-inch and 12 inch plates. “The automatic machines are far more efficient in terms of both running cost and the cost of labour,” adds Vinod. This is because one person can simultaneously work on all six machines since hydraulic pressure is utilised to press the plates in shape and heat applied can be ramped up to 200 degree celsius, speeding up the process. The setup presently has the output of 500 plates per day as stated by Vinod. At an average of 60%, the profit margin for the manufacture of Areca plates is very high. Being a zero waste process in itself, multiple plates can be cut out from a single leaf while the remaining material doubles as fodder for cattle. Moreover, the timely removal of leaves eliminates the threat of fungus attacks on the farm, thus saving a large amount of resources from being spent on fungicides. “There is a huge demand for areca plates in Goa and, with the ban on plastic, it’s only bound to increase,” says Vinod. “My entire production of 500 plates per day is hardly enough to meet the demand from one shop in Mapusa” he adds. The demand for plates is massive, but the supplies are very scarce in the state, which is why most are brought in from places like Tumkur, Sirsi, Sagar and Kumta, among other places. “The demand is so large that more than a hundred manufacturers like me are required to meet the needs of the state,” admits Vinod Barve.
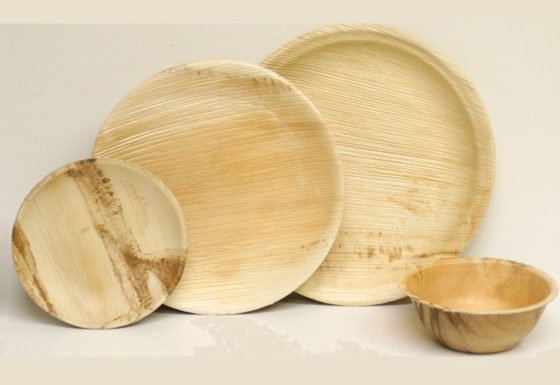
Over time, the plate unit and the agricultural produce yielded enough revenue to diversify. In 2017, the Barves began cashew-processing.
Availing benefits from the Standup India Scheme for lady entrepreneurs and the provisions allowed by the Krishi Credit Card, Anjali Barve started Ganesh Cashews – a cashew-processing plant on their land in Satoda-Valpoi. The plant is set up in a shed and has a workforce of 12 employees, all of whom are ladies. “It gives me a great feeling of fulfillment and happiness to work among our dedicated workforce with camaraderie,” beams Anjali Barve. The processing unit is equipped with a boiler, which is fuelled by firewood. The generated steam from the boiler is passed to a cooker, where the raw cashew nuts are steamed at very high temperatures. This process loosens the nut from the shell as oil oozes to the surface of the outer shell. After that, shells are cut with a specialised electric cutting machine having an output of 120 nuts per minute. The industrial unit is equipped with two of these machines. After the shell has been separated from the nuts, the nuts are polished. This process separates the kin from the nuts and gives it the color and finish that we are familiar with.
The nuts are then segregated into different grades according to their size, integrity, finishing and colour. Once segregated, the nuts are put in a drying machine where they get a crisp texture. After drying, the finished product is sealed and packed off in different quantities for dispatch.
“The total output of the unit is about seven tonnes per year,” says Anjali, “This creates a revenue of over ₹56 lakh,” she adds. The entire running and management of the plant is looked after by Anjali, for which she credits her father Gokuldas Shikerkar who invested in her education, which was uncommon in that time; she holds a Master’s degree in Arts. “Being an all-ladies workforce helps in many ways,” says Anjali, “It instills confidence in our workers and also gives them financial independence,” adds Anjali. Post processing, the cashews are supplied to markets in Mapusa and Panaji as well as factories manufacturing biscuits and chocolates as per their needs.
“When we started, we procured raw cashew nuts worth ₹35 lakh. It generated revenue of ₹56 lakh in the last financial year, we look forward to scaling it further this year” Anjali informs.
The Barves also have a sprawling horticulture business which has been tended to expertly over the years. Looking back, he says, “The major turning point for the business was when we bought a tractor back in 2005. Since most of the plantations are in hilly areas, transportation is the biggest problem. Considering the severe scarcity of labour, the tractor ramped up my marketable produce,” Vinod adds.
Since then, the Barves have only looked forward and are literally enjoying the fruits of their labour